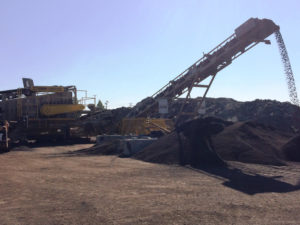
Lafarge produces Aggneo with a mobile crushing plant. Photo courtesy of Lafarge.
The trademark symbol pressed against the product name is somewhat unusual. Not because the little “TM” symbol is a foreign concept, but because it’s rare to see the symbol associated with recycled aggregates.
Yet, the symbol is there next to the name “Aggneo,” a Lafarge trademark for its range of recycled aggregates that launched within the last few years. Lafarge refers to Aggneo as “a range of new generation, high-quality recycled aggregates that meets a wide array of needs for sustainable construction in the civil, industrial, commercial and residential segments.” Aggneo is produced with a mobile crushing plant for the market in Vancouver, British Columbia, Canada.
Not all recycled aggregate is created equal, of course, but the trademark calls extra attention to the Lafarge product. What makes Aggneo unique from other recycled aggregates, and how exactly is Lafarge producing these aggregates?
According to Lafarge, recycled materials are often limited to non-sensitive applications such as general fills. Aggneo, however, is being marketed as “a consistent and reliable alternative to virgin aggregates for a wider range of applications, including base for heavy traffic roads.”
Chen Mei, vice president of Greater Vancouver Aggregate at Lafarge, provided some additional insight about Aggneo. One takeaway she offered is the value of a thorough quality control program.
“The quality and consistency of the recycled material varies considerably,” Mei says. “The different batches of materials can deviate a lot. That’s the nature of the business.”
The major change Lafarge introduced is in the quality control process.
“We do an inspection at the time when the raw material is taken in and also at the time of production. We check regularly on the quality and different parameters to make sure it’s consistent. That’s the biggest difference compared with regular recycled aggregates.”
Specifically, Mei says Lafarge assigns one person to do a thorough inspection of all C&D recyclables as they are received. Deliveries arrive in one particular area of the Lafarge property, and materials that do not meet the company’s quality standard are rejected.
Other portable plant operators can surely relate. As Mei says, if producers are not consistent on the front end of production then they cannot deliver high-performing end products.
In Aggneo’s case, Mei says Lafarge isn’t simply recycling concrete and asphalt rubble. She refers to Aggneo production as “manufacturing,” an approach that sets the bar higher for recycled aggregate production.
“All material has certain limitations,” Mei says. “It’s really our aspiration to optimize our manufacturing process and to make the quality of recycled products as good as virgin aggregate in certain applications.”